
Automatic Round Shape Instant Noodles Production Line
Classification:
Product Introduction
After-sales Service: 10 Years
Warranty: 1year
Product Details
Product profile
The technical characteristics of our company's automated production line for fried cup instant noodles are mainly reflected in the following aspects:
The production line adopts a touch screen operation interface and PLC (Programmable Logic Controller) program control to achieve parameter preset, photoelectric tracking, and variable frequency speed regulation, supporting single machine fine-tuning and full line linkage synchronous control.
-The automatic temperature adjustment system for frying ensures temperature stability, reduces oil content, and improves the yield of genuine products. At the same time, it supports dynamic adjustment of noodle weight without stopping the machine.
-The packaging process integrates automatic feeding, laminating, sealing and other processes, and seamlessly connects with the packaging equipment through a conveyor at the back end, without the need for manual intervention.
2- The production line supports multiple specifications of production, with noodle weights ranging from 50-100 grams, and can be adapted to different shapes such as square (bagged) or circular (cup/bowl).
-The production capacity covers a wide range, with a single shift (8 hours) output ranging from 40000 to 200000 pieces, meeting the needs of large-scale production.
3- Adopt energy-saving technologies to reduce energy consumption, such as using dual axis dual speed technology to improve water powder mixing efficiency and reduce raw material waste in dough machines.
-Optimization of steaming and frying processes: The multi-layer steaming machine extends the steaming time to 150 seconds, combined with soaking and flavor technology to enhance the taste; The frying machine reduces fuel consumption through temperature control, and some equipment is also equipped with an oil filtration system.
4- The equipment and food contact parts are made of stainless steel and food grade materials, which comply with hygiene standards
5- Realize full process automation from raw material supply to packaging and warehousing, including salt water mixing, kneading, curing, rolling, steaming, sorting, frying, cooling and other processes, reducing manual intervention.
6- Provide installation and debugging, as well as personnel training, with a one-year free warranty for some, to reduce user operational risks.
summarize
The core advantages of the automated production line for fried cup instant noodles lie in intelligent control, flexible adaptability, efficient production capacity, and hygiene and safety. Through technological integration, the entire process from raw materials to finished products is automated, while also considering energy conservation and quality stability. The configuration differences among different manufacturers are mainly reflected in production capacity, energy consumption control, and additional functions. Users can choose the appropriate model according to their actual needs.
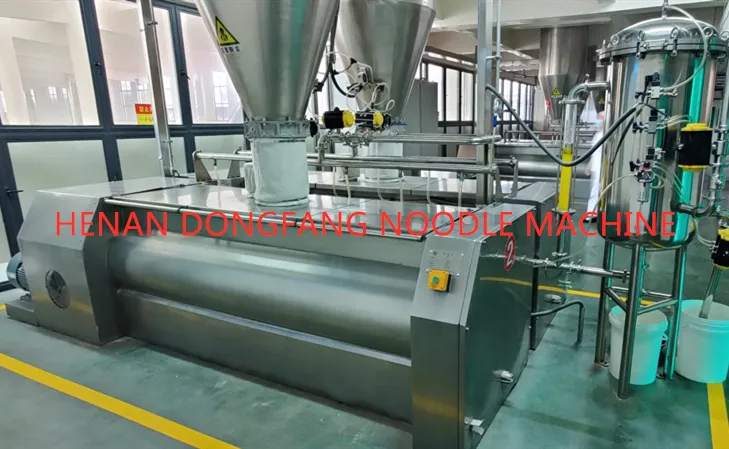
Dual-axis mixing machine
Standard :mixer body length 2000, capacity 300kg/ time
Material :304 stainless steel:mixer body, paddle, cover board
Function: mixer can supply flour and water, knead dough and feed at same time. The dough and the flour is well blended and in slight color variation.
Rollers
Function:The new type Roller machine adopts a brand-new appearance design, which is beautiful and novel, giving people a completely new feeling. Adopting four-axis feeding, smooth feeding, ensuring the integrity of the noodle sheet, and excellent sheet forming effect; especially the effective combination of photoelectric tracking and automatic sheet feeding, which greatly reduces labor intensity; The safety of operation, single-roller independent transmission, automatic adjustment the speed of the dough sheet, and electric adjustment the thickness of the dough sheet. The entire pressing process is smooth and simple, and the pressed dough sheet is extremely tough.
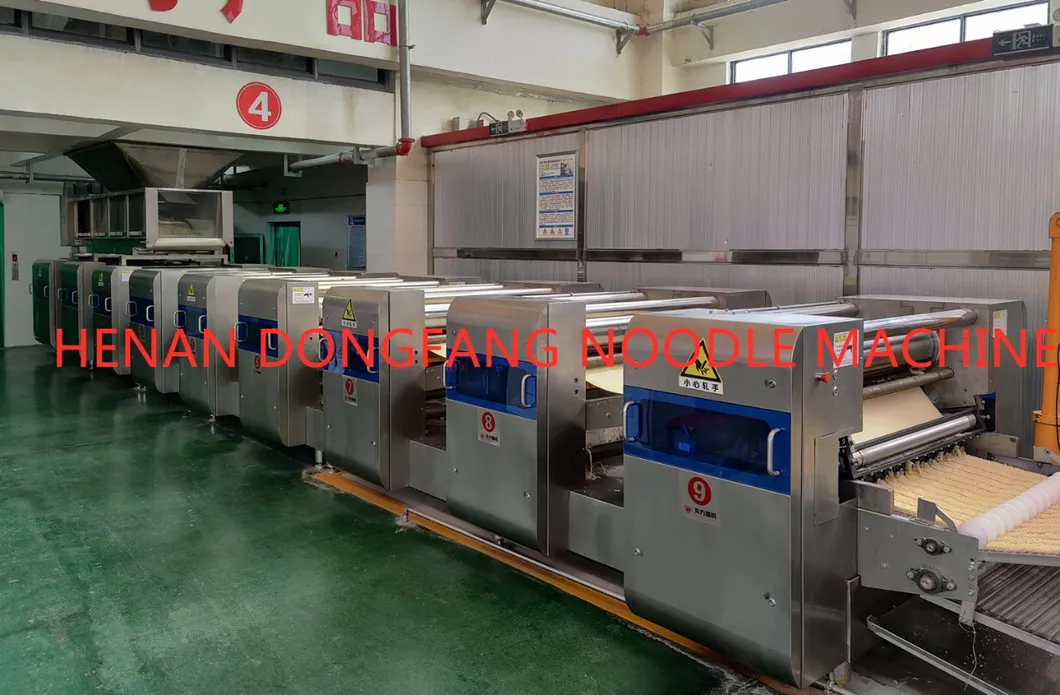
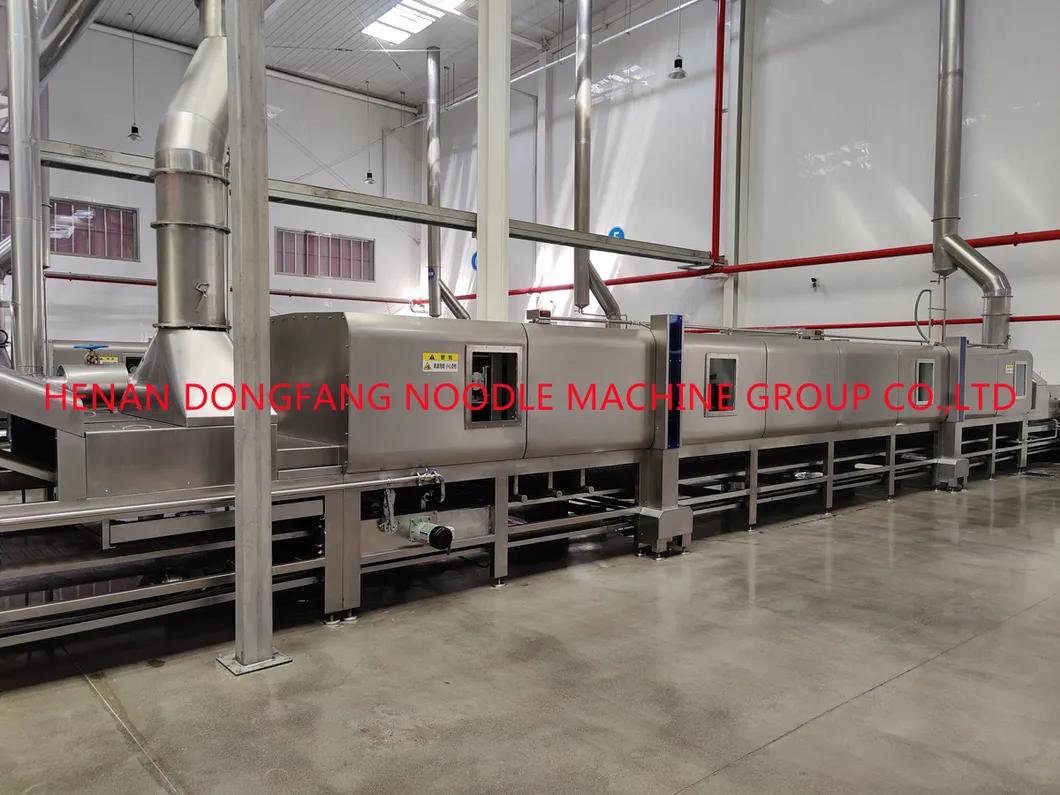
Steamer
Function:Water-sealed multi-layer noodle steamer is a new product developed by our company. It has a smooth appearance and is water-tight and air-tight, which solves the problem that the traditional multi-layer steamer must be sealed with rubber strips. The internal steam pipes are carefully arranged to ensure the gelatinization effect and save a lot of steam. The upper cover can be lifted open. Make it easy and fast internal sanitation and cleaning.
Noodle cutting and dividing machine
Function:The steamed noodles are cut to a fixed length after being sprayed bywaterfall and with three times stretching, and then fall into the noodle box through the sliding floating bucket. The noodles can be stretched for three times to basically straighten the noodles, which provides good conditions for the automatic shaping machine in the subsequent process. The polymer splitter completely separates the noodles, and the new floating bucket can ensure that each noodle accurately falls into the center of the noodle box.
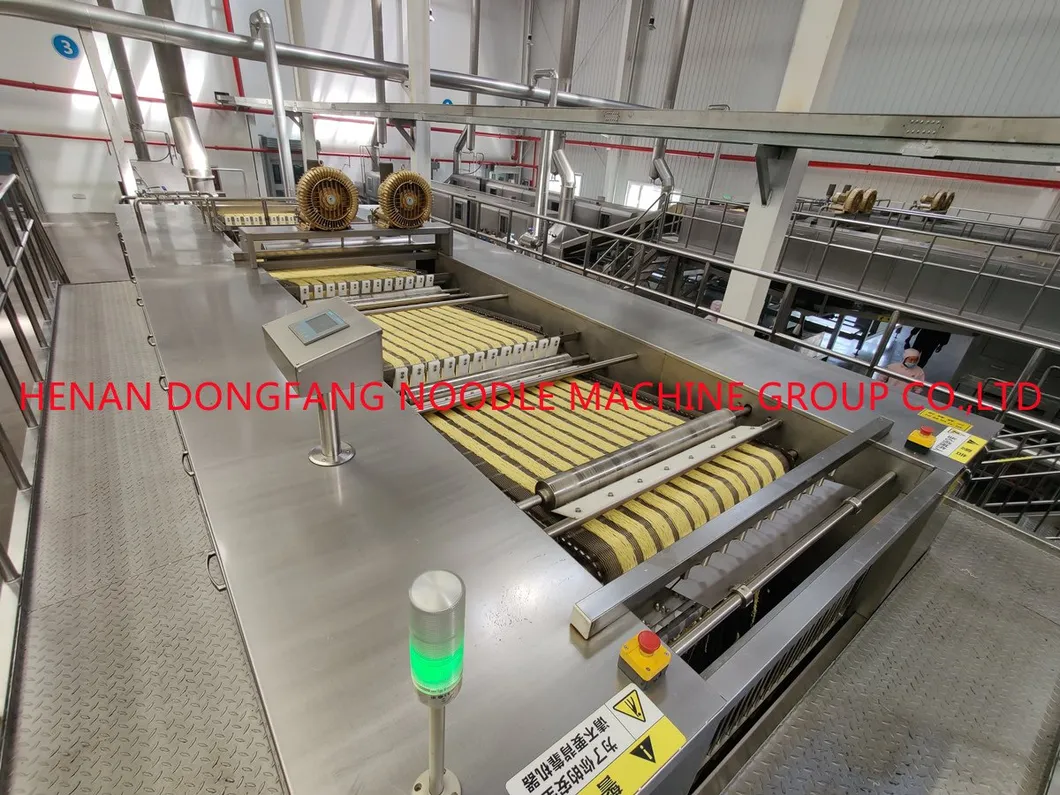
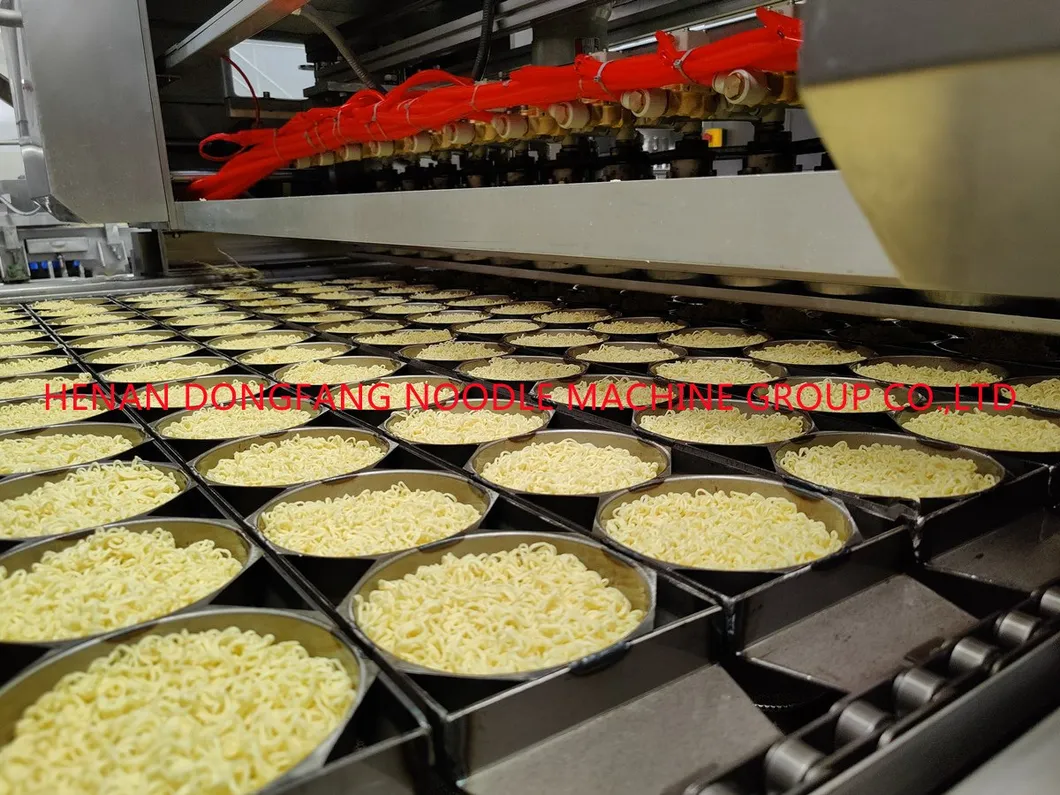
Round noodle shaping blowing machine
Function:The automatic air blowing and shaping machine is a product designed to replace labor. The rotating head rotates while blowing air to achieve the purpose of blowing and shaping the noodles. The shaping process is fully automated, stable and reliable.
Fryer
function:The fryer is the most critical equipment for producing instant noodles. 2-3% lower than similar products, which reduces production costs and improves efficiency; multi-zone oil inlet and tube-in-tube injection ensures that the temperature of the oil pan is uniform, and the color of the noodles after the fried is consistent.The noodle cakes are arranged neatly by the arranging machine and then pushed into the air cooler
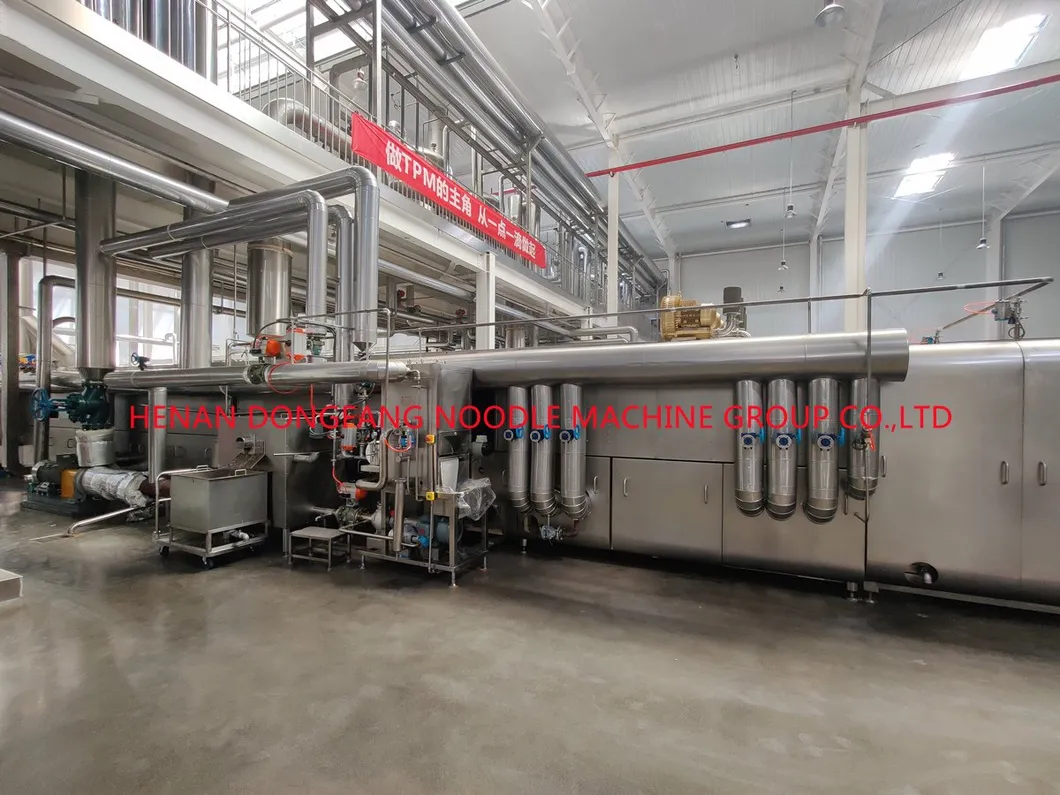
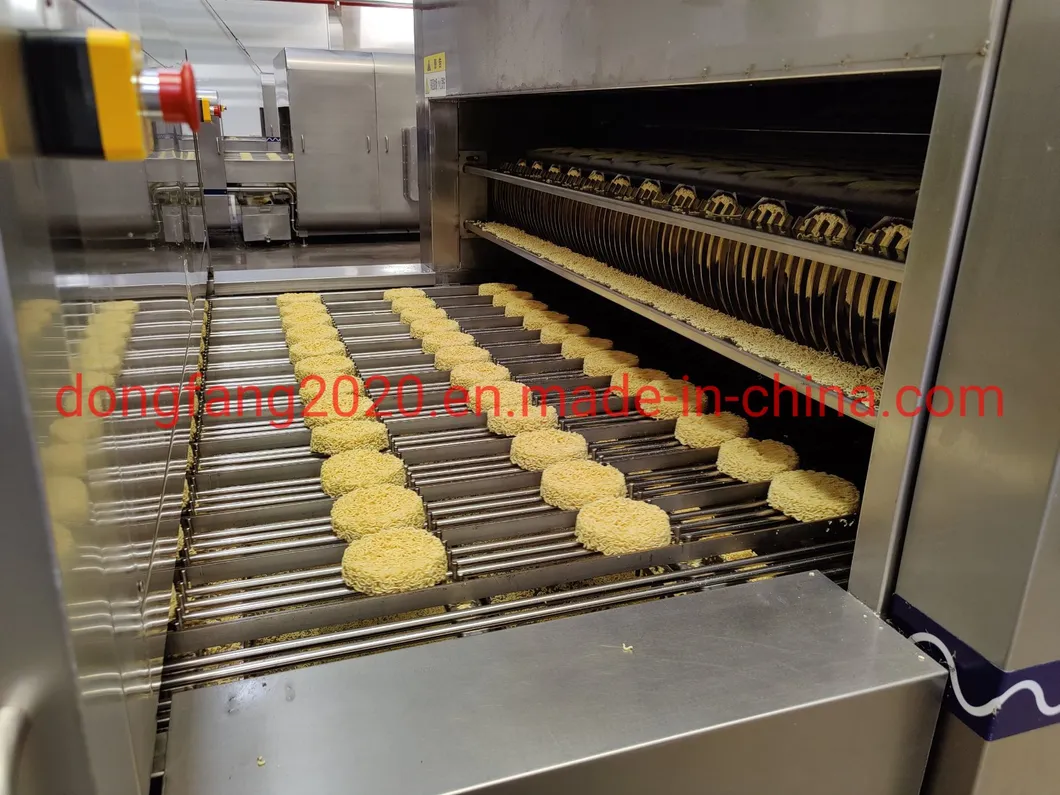
Arranging machine
Function:
The arranging bar carries the noodles, which runs smoothly, neatly, and sanitarily.
Cooling machine
Function:The noodles enter the air-cooler, and they are blown quickly to cool down. Beautiful and smooth appearance, almost perfect internal design, overall, stylish and completely new. Two blowers on one side send air in, and an exhaust fan on the top exhausts the hot air outside. The arranging bar carries the noodles, which runs smoothly, neatly, and sanitarily.
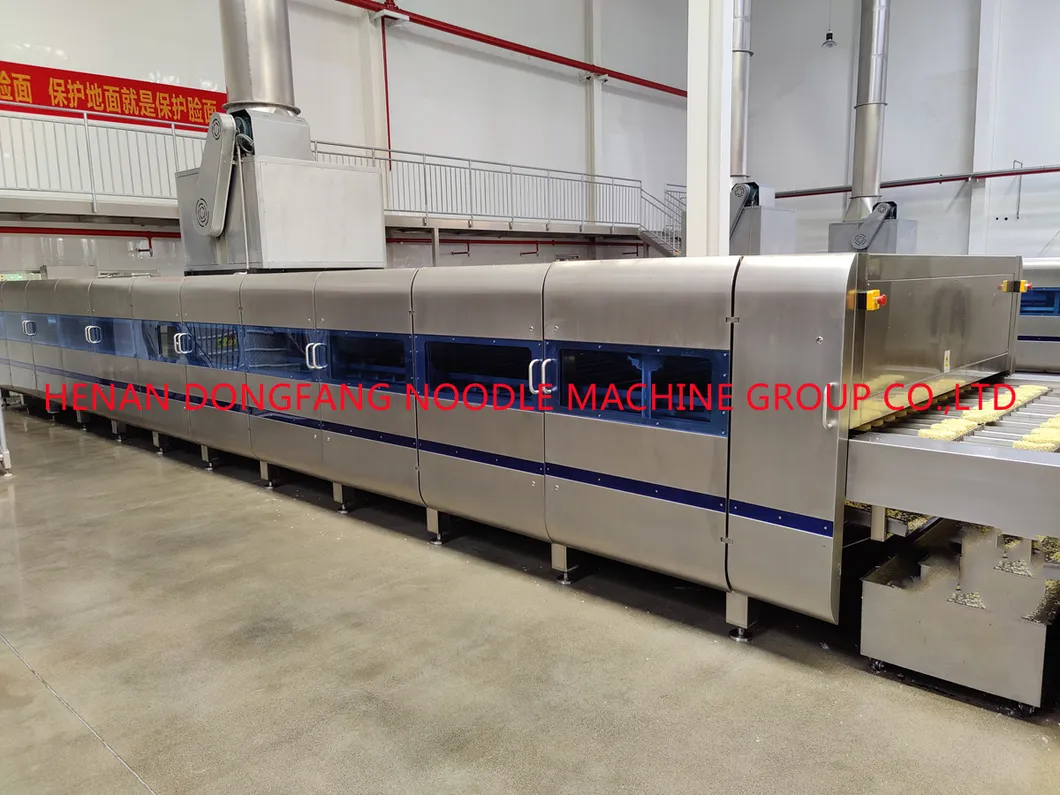
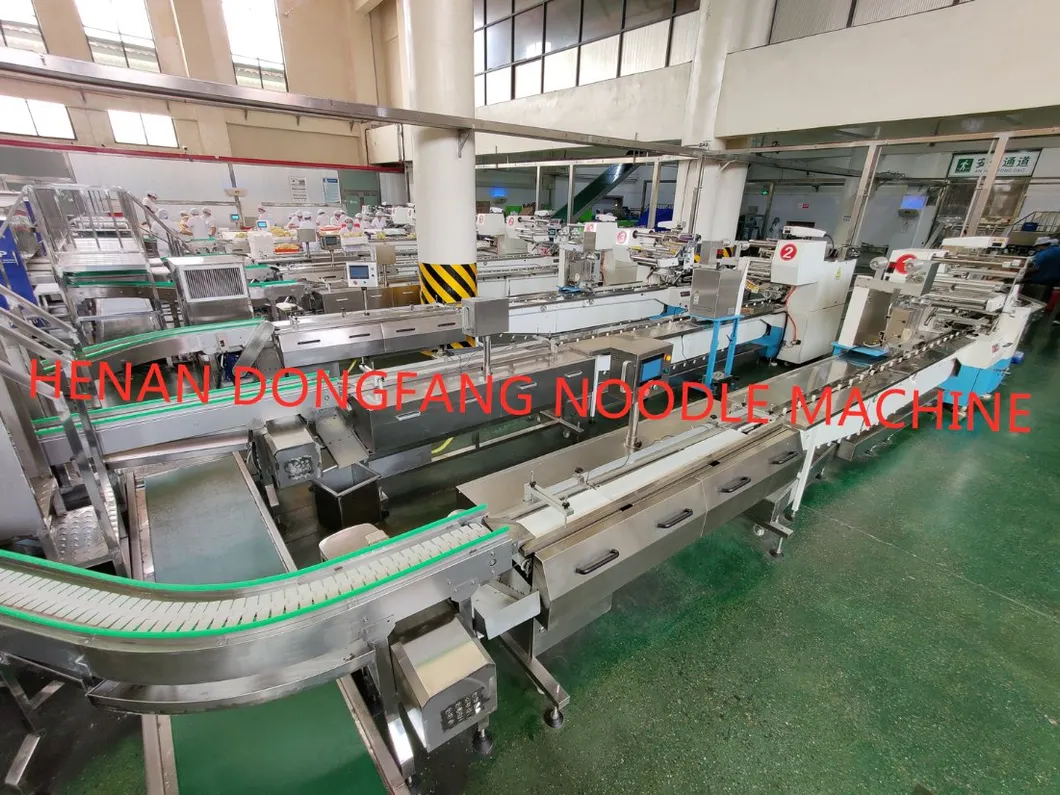
Distributing and checking conveyor
Function:The cooled noodle cake slides down to the conveyor belt through the T-shaped plate, and then enters the packaging machine into several single rows through the distribution strip. The packaging machine adopts frequency control, which has the characteristics of high packaging speed, stable operation and convenient operation.
Parameter
model number | capacity | Power | Steam consumption | Workshop for single layer steamer dimension(m) | Workshop for 3 layer steamer dimension(m) | Workers |
BFP-200 | 40000/8H | 45KW | 1200-1300KG/H | 70*5*4 | 50*5*4 | 4 |
BFP-300 | 60000/8H | 56 KW | 1200-1400KG/H | 75*5*4 | 60*5*4 | 4 |
BFP-400 | 110000/8H | 83 KW | 1800-2000KG/H | 100*6*4 | 75*6*4 | 4 |
BFP-500 | 140000/8H | 90 KW | 1800-2100KG/H | 100*6*4 | 75*6*4 | 4 |
BFP-600 | 160000/8H | 106 KW | 2000-2200KG/H | 100*7*4.5 | 80*7*4.5 | 5 |
BFP-700 | 200000/8H | 114 KW | 2400-2600KG/H | 110*8*4.5 | 80*8*4.5 | 5 |
BFP-800 | 230000/8H | 125 KW | 2600-2800KG/H | 110*8*4.5 | 90*8*4.5 | 5 |
workers:( not including packaging workers ) |
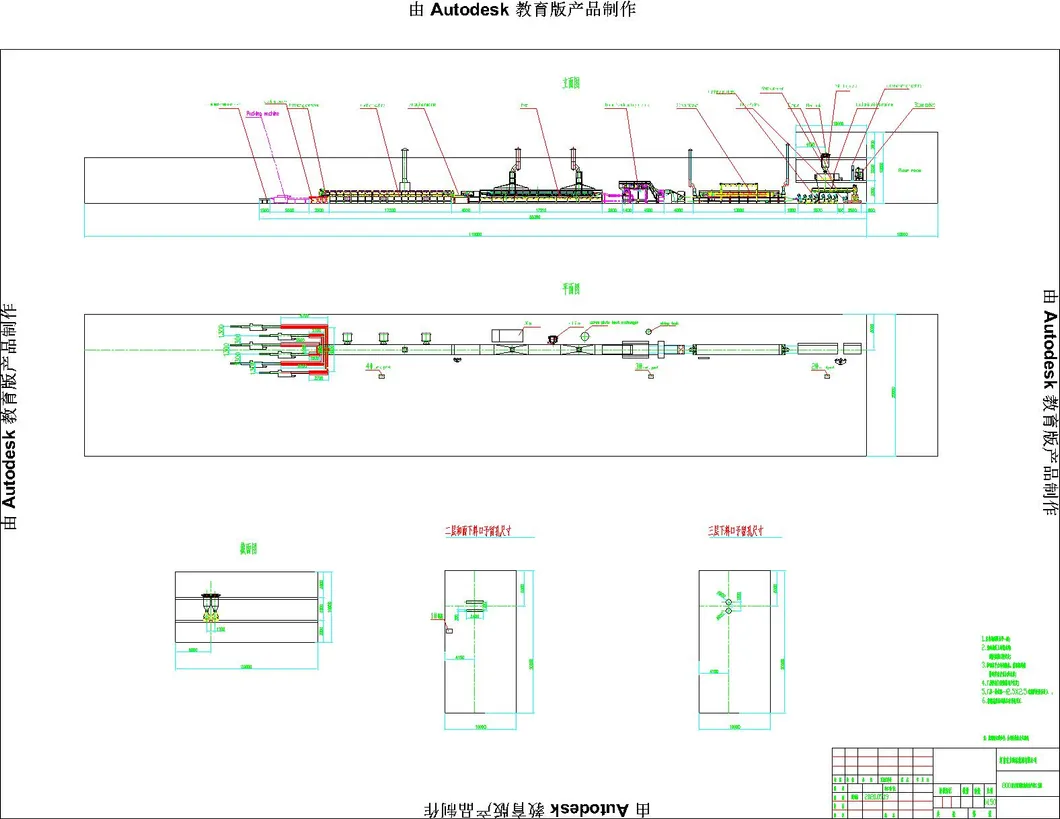
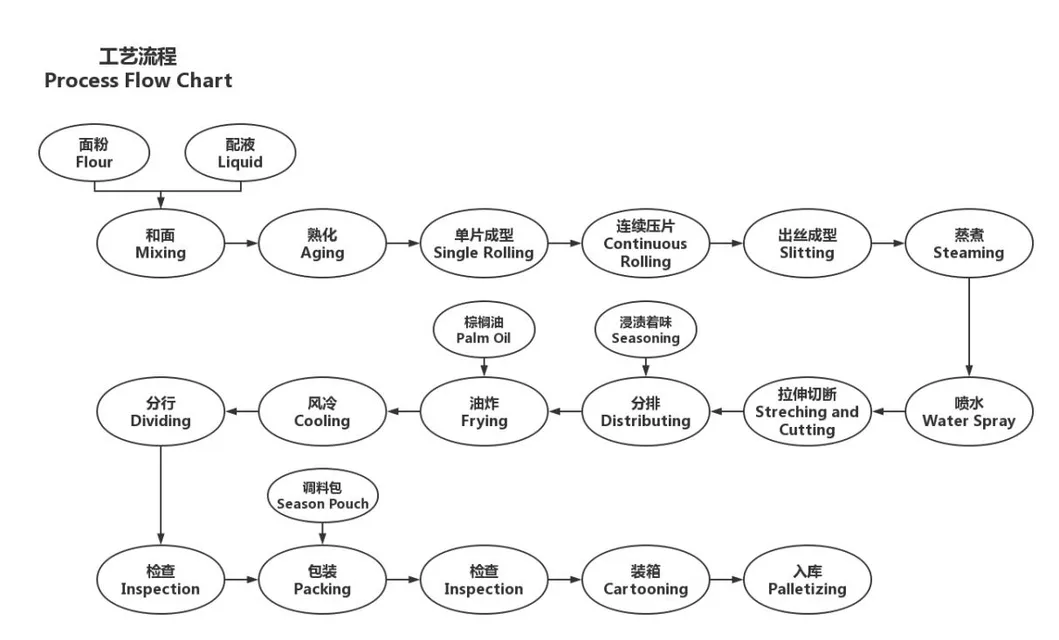
Key words:
Layout
Please leave us a message
Feel free to leave your contact information for more information